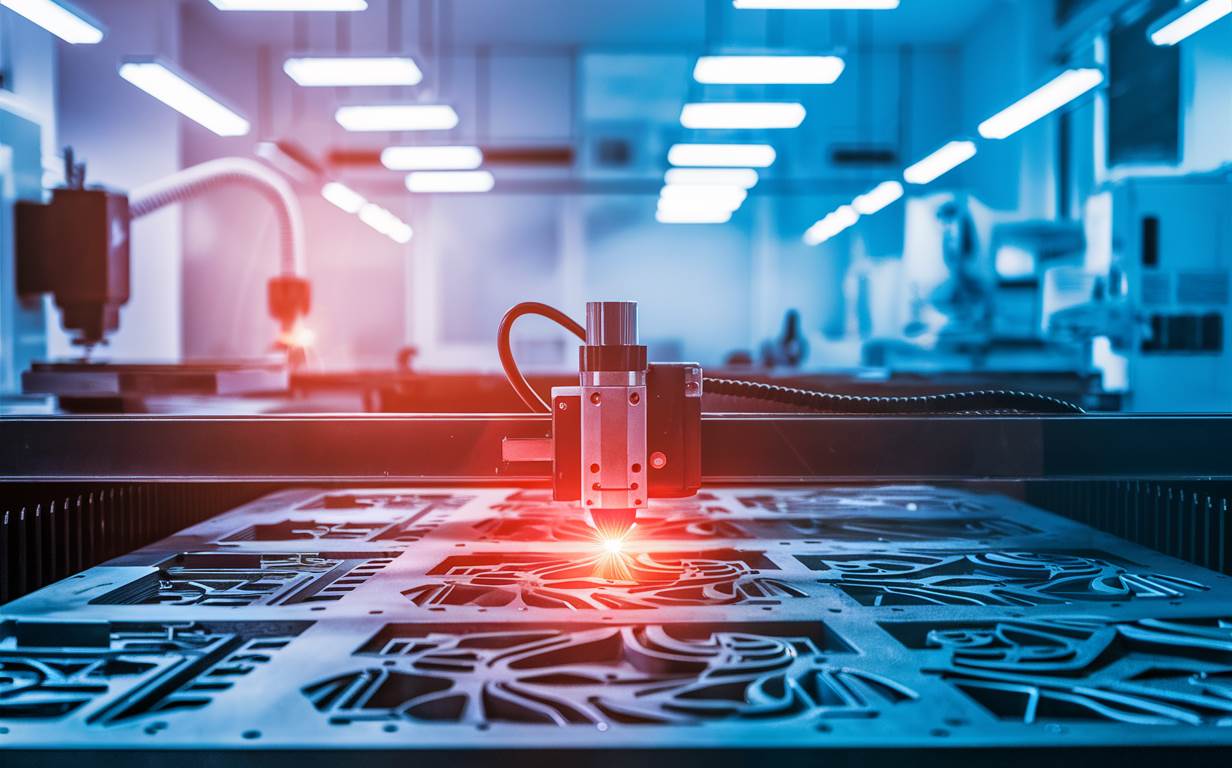
Optyczne technologie cięcia to kluczowy element współczesnej przemysłowej produkcji, umożliwiający precyzyjne i skuteczne przycinanie różnorodnych materiałów. Istnieje kilka głównych metod cięcia optycznego, które znalazły zastosowanie w różnych branżach.
Jedną z najpopularniejszych metod jest laserowe cięcie optyczne. Laser wykorzystywany w tym procesie emituje skoncentrowane światło o wysokiej mocy, które jest skierowane na materiał do cięcia. Dzięki temu laser może przeprowadzać cięcia o dużych precyzji i dokładności, nawet w bardzo cienkich materiałach. Technologia laserowa jest wykorzystywana między innymi w przemyśle motoryzacyjnym do cięcia blachy oraz w przemyśle elektronicznym do produkcji obwodów drukowanych.
Kolejną ważną metodą jest cięcie wodą, które również można zakwalifikować jako optyczne ze względu na zastosowanie zaawansowanych technologii światłowodowych do przesyłania i skupiania wiązki. Proces cięcia wodą polega na wykorzystaniu strumienia wody pod wysokim ciśnieniem, często z dodatkiem abrasywnego materiału jak granat piaskowy, który wzmacnia zdolność przecinania materiałów takich jak metal czy kamień.
Plazmowe cięcie optyczne jest kolejną technologią używaną głównie do cięcia metali, gdzie wykorzystuje się strumień plazmy jonizowanej do topienia i usuwania materiału z przycinanego elementu. Metoda ta jest ceniona za szybkość oraz możliwość cięcia materiałów o większej grubości.
Podstawy technologii cięcia optycznego
Technologia cięcia optycznego to zaawansowana metoda wykorzystywana do precyzyjnego przecinania materiałów za pomocą skoncentrowanej wiązki laserowej. W porównaniu do tradycyjnych metod cięcia, takich jak mechaniczne noże czy piły, cięcie optyczne oferuje znacznie wyższą dokładność oraz możliwość obróbki różnych materiałów, w tym metali, tworzyw sztucznych, a nawet tkanin.
Laser jako narzędzie tnące jest sercem technologii cięcia optycznego. W zależności od typu lasera, różnią się one długością fali i mocą, co determinuje ich zastosowanie do różnych materiałów. Na przykład:
- Lasery CO2 – często używane do cięcia tworzyw sztucznych, drewna i tkanin.
- Lasery włóknowe – idealne do cięcia metali, takich jak stal i aluminium.
- Lasery Nd:YAG – stosowane głównie w przemyśle metalowym do cięcia i spawania.
Technologia cięcia optycznego wykorzystuje proces fototermiczny, w którym energia laserowa jest absorbowana przez materiał, powodując jego lokalne nagrzewanie i topnienie lub odparowanie. Precyzyjne sterowanie laserem pozwala na mikroskopijne cięcia, co jest nieosiągalne dla konwencjonalnych metod.
Kluczowe elementy systemu cięcia optycznego to:
- Źródło lasera – generuje wiązkę laserową o odpowiednich parametrach.
- Układ optyczny – soczewki i zwierciadła skupiające wiązkę na powierzchni materiału.
- Stół roboczy – platforma, na której umieszczany jest materiał do cięcia, często wyposażona w systemy chłodzenia.
- Sterowanie CNC – komputerowy system sterowania, który precyzyjnie kieruje ruchem lasera wzdłuż zaprogramowanej ścieżki.
Przykładowe zastosowania cięcia optycznego obejmują:
Zastosowanie | Opis |
---|---|
Elektronika | Precyzyjne wycinanie mikrostruktur w płytkach drukowanych i innych komponentach. |
Medycyna | Produkcja narzędzi chirurgicznych i implantów o wysokiej dokładności. |
Motoryzacja | Cięcie i formowanie części karoserii i podzespołów silnikowych. |
Moda | Wycinanie skomplikowanych wzorów w tkaninach i skórze. |
Jakie materiały można obrabiać za pomocą cięcia laserowego?
Technologia cięcia laserowego umożliwia precyzyjne obrabianie wielu różnych materiałów, co czyni ją wszechstronną metodą w przemyśle i rzemiośle. Oto główne materiały, które można efektywnie obrabiać za pomocą cięcia laserowego:
Materiał | Zastosowania | Zalety cięcia laserowego |
---|---|---|
Metale | Stal, aluminium, miedź | Możliwość cięcia różnych grubości materiałów, wysoka precyzja, brak konieczności dodatkowego wykończenia krawędzi |
Drewno | Sklejka, drewno lite | Szybkość i dokładność cięcia, możliwość wycinania skomplikowanych wzorów, minimalizacja odpadów materiałowych |
Tworzywa sztuczne | Poliwęglany, akryl, tworzywa inżynieryjne | Czyste i gładkie krawędzie, minimalne uszkodzenia powierzchni, precyzyjne detale |
Tkaniny | Bawełna, filc, włókniny | Bezspoinowe cięcie, możliwość wycinania skomplikowanych wzorów, brak rozwarstwień materiału |
Szkło | Laminowane, hartowane | Precyzyjne cięcie, brak pęknięć i uszkodzeń, możliwość cięcia na kształt |
Cięcie laserowe jest również stosowane do obróbki kamienia (takiego jak granit czy marmur), pianki (np. poliuretanowej do pakowania), oraz gumy (do produkcji uszczelek i elementów przemysłowych).
Zaawansowane zastosowania cięcia laserowego
Cięcie laserowe stało się nieodzowną technologią w wielu dziedzinach przemysłu dzięki szybkości, precyzji i możliwości automatyzacji. Jednym z kluczowych aspektów rozwoju tej technologii są zaawansowane zastosowania, które otwierają nowe możliwości produkcji i obróbki materiałów.
Technologia cięcia laserowego jest szczególnie skuteczna w produkcji optyki laserowej. Soczewki laserowe, które są kluczowym elementem układów optycznych, wymagają precyzyjnego kształtowania, którego dostarcza cięcie laserowe. Dzięki tej technologii możliwe jest nie tylko uzyskanie idealnych kształtów, ale także minimalizacja zabrudzeń i uszkodzeń powierzchni, co jest kluczowe dla efektywności i trwałości soczewek laserowych.
Kolejnym innowacyjnym zastosowaniem jest cięcie rur za pomocą laserów. Technologia ta pozwala na precyzyjne cięcie rur o różnych kształtach i średnicach, co jest niezbędne w przemyśle motoryzacyjnym, budowlanym oraz w produkcji maszyn. Laserowa obróbka rur umożliwia także dodatkowe operacje, takie jak cięcie otworów czy wykańczanie krawędzi, co znacząco zwiększa wszechstronność i użyteczność tej technologii.
W dziedzinie elektroniki cięcie laserowe znalazło swoje zastosowanie w produkcji mikroelementów i układów scalonych. Precyzyjność i szybkość cięcia pozwalają na tworzenie mikroskopijnych detali bez ryzyka ich uszkodzenia czy zniekształcenia. Technologia ta jest nieoceniona w produkcji nowoczesnych urządzeń elektronicznych, gdzie każdy milimetr i każda mikrosekunda są kluczowe dla efektywności i wydajności.