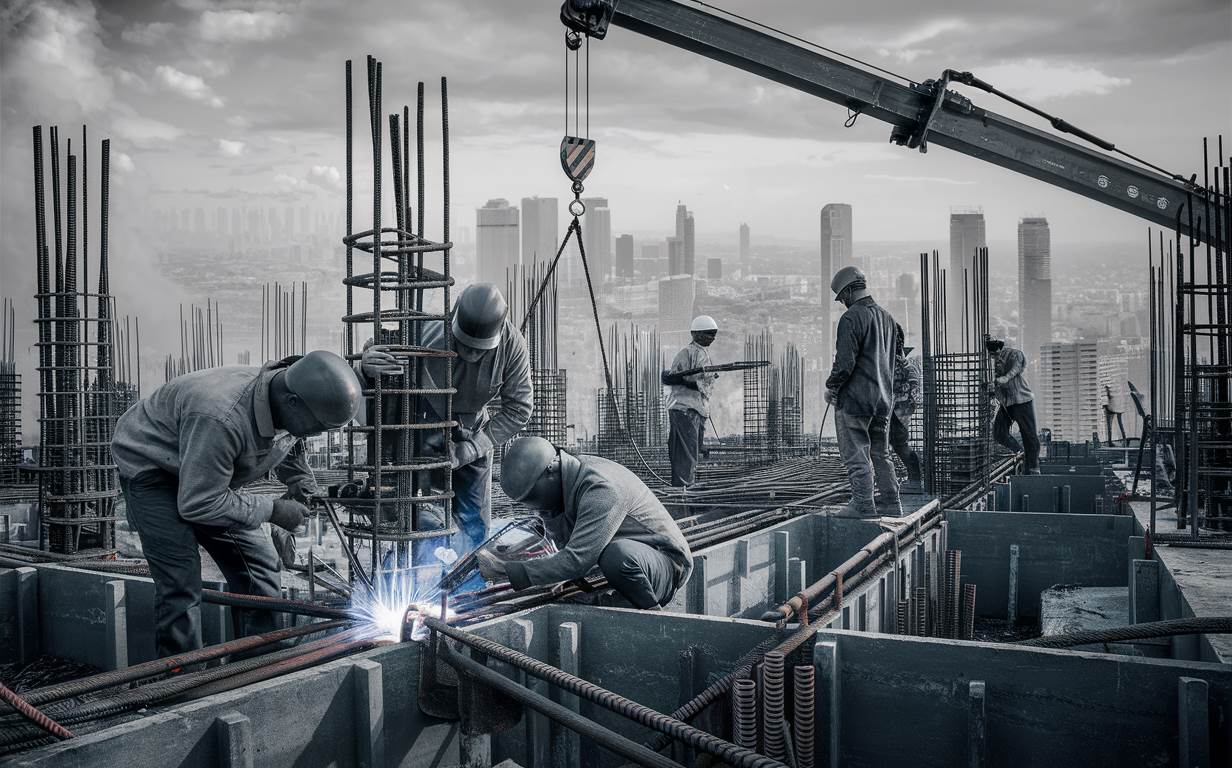
Spawanie zbrojenia fundamentów to kluczowy proces w budownictwie, który zapewnia trwałość i stabilność konstrukcji. Aby prawidłowo przeprowadzić ten proces, należy przestrzegać kilku podstawowych kroków i zasad.
Na początku należy przygotować miejsce pracy. Obejmuje to oczyszczenie zbrojenia z rdzy, tłuszczu i innych zanieczyszczeń, które mogą wpłynąć na jakość spawu. Najlepiej jest używać szczotek drucianych lub szlifierek kątowych. Ważne jest również, aby upewnić się, że wszystkie elementy zbrojenia są odpowiednio przycięte i dopasowane do projektu.
Przed przystąpieniem do spawania, należy dobrać odpowiednią metodę spawania. Najczęściej stosowane metody to spawanie łukowe (MMA) oraz spawanie półautomatyczne (MAG). Wybór metody zależy od grubości prętów zbrojeniowych oraz wymagań projektowych.
Podczas spawania zbrojenia fundamentów, istotne jest, aby używać odpowiednich elektrod lub drutów spawalniczych. Dla spawania łukowego, zalecane są elektrody rutylowe, które charakteryzują się dobrą stabilnością łuku oraz łatwością w obsłudze. W przypadku spawania półautomatycznego, stosuje się druty spawalnicze w osłonie gazowej (np. CO2 lub mieszanka gazów), co zapewnia lepszą jakość spoiny.
Przy spawaniu prętów zbrojeniowych, ważne jest utrzymanie odpowiednich parametrów spawania, takich jak prąd spawania, napięcie oraz prędkość podawania drutu. Parametry te powinny być dostosowane do grubości prętów oraz rodzaju spawania. Należy również pamiętać o odpowiednim przygotowaniu połączeń spawalniczych. Pręty powinny być ułożone w taki sposób, aby zapewnić dobrą penetrację spawu i minimalizować naprężenia wewnętrzne.
Podczas samego procesu spawania, należy zwrócić uwagę na technikę prowadzenia spoiny. Spoina powinna być równomierna, bez przerw i pęcherzy powietrza. Dla większej pewności, spoiny powinny być kontrolowane wizualnie oraz przy użyciu metod nieniszczących, takich jak badania magnetyczno-proszkowe czy ultradźwiękowe.
Po zakończeniu spawania, kluczowe jest schłodzenie spoin w sposób kontrolowany. Zbyt szybkie schłodzenie może prowadzić do pęknięć, dlatego zaleca się stopniowe schładzanie, na przykład za pomocą materiałów izolacyjnych.
Ostatnim etapem jest inspekcja i odbiór techniczny spoin. Każda spoina powinna być dokładnie sprawdzona pod kątem wad oraz zgodności z projektem. Niezbędne jest również sporządzenie dokumentacji technicznej, która będzie potwierdzać jakość wykonanych prac spawalniczych.
Techniki spawalnicze fundamentów
Spawanie fundamentów jest kluczowym procesem w budownictwie, wymagającym precyzyjnych technik i wysokiej jakości wykonania. Spawanie jest stosowane do łączenia elementów konstrukcyjnych w sposób trwały i odporny na obciążenia.
Podczas spawania fundamentów najczęściej używane są metody spawania łukowego, takie jak spawanie elektryczne i gazowe. Procesy te umożliwiają precyzyjne kontrolowanie temperatury oraz zabezpieczają połączenia przed uszkodzeniami mechanicznymi.
Spawanie elektryczne wykorzystuje łuk elektryczny do topienia materiału w strefie spawania. Jest to szybka metoda, która zapewnia mocne połączenia między elementami fundamentów. W przypadku spawania elektrycznego istotne jest odpowiednie zabezpieczenie przed wyładowaniami elektrycznymi oraz precyzyjne ustawienie prądowe i napięciowe.
Spawanie gazowe opiera się na wykorzystaniu palnika gazowego do generowania wysokiej temperatury niezbędnej do spawania. Metoda ta jest szczególnie efektywna przy spawaniu elementów grubych oraz w warunkach, gdzie dostęp do źródeł prądu elektrycznego może być ograniczony.
Podczas spawania fundamentów niezwykle istotne jest zachowanie odpowiednich parametrów spawalniczych, takich jak prędkość spawania, strumień gazu ochronnego, oraz rodzaj używanej elektrody. Dobór odpowiedniego materiału spoinowego jest kluczowy dla trwałości i wytrzymałości połączeń spawalniczych.
Metoda spawania | Zalety | Wady |
---|---|---|
Spawanie elektryczne | Szybkość i precyzja | Wymaga źródła prądu |
Spawanie gazowe | Wykorzystanie dostępnego gazu | Wyższe koszty materiałowe |
W przypadku spawania fundamentów istotne jest również zapewnienie właściwych warunków ochrony podczas procesu spawania. Odpowiednie wentylacje, zabezpieczenia przed ogniem oraz stosowanie osobistej ochrony spawacza są nieodzownymi elementami pracy.
Bezpieczeństwo podczas spawania
Prace budowlane często wymagają zastosowania technik spawalniczych, które są nieodzownym elementem w konstrukcji metalowych ram i konstrukcji. Aby zapewnić bezpieczeństwo podczas spawania, niezbędne jest przestrzeganie szeregu środków ostrożności oraz znajomość potencjalnych zagrożeń związanych z tym procesem.
Zagrożenia podczas spawania mogą obejmować ryzyko poparzeń, urazów oczu, zatrucia gazami oraz pożarów. Każde z tych niebezpieczeństw wymaga szczególnej uwagi i odpowiednich środków ochrony osobistej.
Zagrożenie | Środki ochrony |
---|---|
Poparzenia | Używanie odzieży ognioodpornej, rękawic spawalniczych, izolacji przeciwwybuchowej. |
Urazy oczu | Stosowanie okularów ochronnych lub osłon spawalniczych, które zapewniają odpowiednią ochronę przed iskrzeniem i promieniowaniem UV. |
Zatrucia gazami | Praca w dobrze wentylowanych miejscach, stosowanie odpowiednich filtrów przeciwgazowych w maskach spawalniczych. |
Pożary | Przechowywanie materiałów łatwopalnych w odpowiednich odległościach od obszaru spawania, stosowanie gaśnic i innych środków gaśniczych. |
Podczas spawania należy również pamiętać o prawidłowym uziemieniu oraz kontrolowaniu temperatury otoczenia, aby minimalizować ryzyko pożarów. Dodatkowo, szkolenie pracowników w zakresie bezpiecznego spawania oraz regularne przeprowadzanie inspekcji sprzętu spawalniczego są kluczowe dla utrzymania wysokich standardów bezpieczeństwa.
Zastosowanie spawania pod wodą
Spawanie pod wodą jest kluczową metodą w pracach podwodnych, szczególnie w branży offshore oraz w konserwacji i naprawie konstrukcji morskich. Spawanie pod wodą umożliwia przeprowadzanie napraw i budowę nowych struktur bez konieczności ich wyciągania na powierzchnię, co znacząco obniża koszty oraz czas realizacji projektów. Technika ta jest niezbędna w wielu sektorach przemysłu, od budowy platform wiertniczych po naprawy kadłubów statków i konstrukcji portowych.
Główne zastosowania spawania pod wodą to:
- Naprawy konstrukcji stalowych: Mosty, molo, fundamenty wież wiatrowych i inne stalowe struktury mogą ulegać uszkodzeniom z powodu korozji lub uderzeń. Spawanie pod wodą pozwala na ich szybkie i efektywne naprawy.
- Instalacje rurociągów: Rurociągi transportujące ropę, gaz lub wodę są często montowane na dnie morskim. Techniki spawania pod wodą są niezbędne do łączenia sekcji rurociągów oraz naprawy ewentualnych uszkodzeń.
- Naprawa kadłubów statków: Uszkodzenia kadłubów mogą być spowodowane kolizjami, korozją lub innymi czynnikami. Spawanie pod wodą umożliwia przeprowadzenie napraw bez potrzeby dokowania statku, co jest czasochłonne i kosztowne.
- Budowa i konserwacja platform wiertniczych: Platformy wiertnicze są narażone na ekstremalne warunki środowiskowe. Regularne spawanie pod wodą jest konieczne do utrzymania ich integralności strukturalnej.
Techniki spawania pod wodą można podzielić na dwie główne kategorie: spawanie mokre i spawanie suche. Każda z tych technik ma swoje zalety i wady oraz różne zastosowania w zależności od warunków pracy i wymagań projektu.
Technika | Opis | Zalety | Wady |
---|---|---|---|
Spawanie mokre | Proces spawania odbywa się bezpośrednio w wodzie, przy użyciu specjalnych elektrod i sprzętu. | Elastyczność, szybka realizacja, niższe koszty. | Niższa jakość spoin, większe ryzyko dla nurków. |
Spawanie suche | Proces spawania odbywa się w komorze, która jest osuszona z wody i wypełniona gazem ochronnym. | Wysoka jakość spoin, bezpieczniejsze warunki pracy. | Wyższe koszty, skomplikowana instalacja komór. |
Sprzęt używany do spawania pod wodą obejmuje specjalne elektrody do spawania mokrego, które są pokryte warstwą ochronną, zapobiegającą szybkiemu rozpuszczaniu się w wodzie. W przypadku spawania suchego używa się zaawansowanych komór hiperbarycznych, które umożliwiają spawaczom pracę w kontrolowanych warunkach, mimo obecności wody wokół komory. Ważnym elementem wyposażenia są również systemy komunikacji i bezpieczeństwa, które umożliwiają stały kontakt nurka z zespołem na powierzchni oraz monitorowanie warunków pracy.
Jak zapewnić trwałość konstrukcji
Podstawą trwałości konstrukcji jest solidna budowa fundamentów. Fundamenty pełnią kluczową rolę w rozkładaniu obciążeń konstrukcji na grunt, zapewniając stabilność i odporność na działanie czynników zewnętrznych. Aby zapewnić, że fundamenty będą spełniały swoją funkcję przez długie lata, należy zwrócić uwagę na kilka istotnych aspektów.
Przede wszystkim, wykonanie fundamentów powinno być precyzyjne i zgodne z odpowiednimi normami budowlanymi. Głębokość fundamentów oraz rodzaj materiału użytego do ich budowy muszą być dobrze dobrane do specyficznych warunków gruntowych panujących na miejscu budowy. W tabeli poniżej przedstawiono przykładowe wymagania dotyczące głębokości fundamentów w zależności od rodzaju gruntu:
Rodzaj gruntu | Głębokość fundamentów |
---|---|
Grunt piaskowy | 1,5 – 2 metry |
Grunt gliniasty | 2 – 3 metry |
Grunt bagrowy | 1 – 1,5 metra |
Kolejnym istotnym aspektem jest wodoodporność fundamentów. Należy zadbać o odpowiednie zabezpieczenie przed wilgocią i wodą gruntową, aby uniknąć degradacji materiałów konstrukcyjnych. Stosowanie izolacji przeciwwilgociowej oraz zastosowanie odpowiednich materiałów hydroizolacyjnych jest kluczowe dla długowieczności fundamentów.
Regularna inspekcja stanu technicznego fundamentów również odgrywa ważną rolę. Konieczne jest monitorowanie ewentualnych uszkodzeń czy oznak osiadania gruntu, co pozwala na szybką reakcję i konieczne naprawy, zapobiegając poważnym problemom w przyszłości.
Kontrola jakości w spawaniu
Jakość w spawaniu odgrywa kluczową rolę w inżynierii budowlanej, zapewniając integralność konstrukcji i bezpieczeństwo użytkowników. Procesy kontroli jakości muszą być ściśle monitorowane i dokumentowane, aby zapewnić zgodność z wymaganiami technicznymi i normami bezpieczeństwa.
Podstawowe metody kontroli jakości w spawaniu obejmują wzrokową ocenę spoin, badania nieniszczące oraz testy mechaniczne. Wzrokowa ocena jest pierwszym etapem, gdzie inspektorzy analizują spoiny pod kątem defektów takich jak pęknięcia, nadmiar metalu czy wtrącenia. Badania nieniszczące takie jak testy ultradźwiękowe lub penetracyjne umożliwiają wykrycie wewnętrznych defektów bez niszczenia spoiny.
Testy mechaniczne, takie jak testy na wytrzymałość i twardość, oceniają fizyczne właściwości spawanych materiałów. Dzięki tym testom można ustalić, czy spoina spełnia wymagania projektowe pod względem wytrzymałości na rozciąganie, gięcie czy uderzenia.
Proces kontroli jakości w spawaniu często obejmuje także aspekty technologiczne. Parametry spawania takie jak prąd, naprężenie i prędkość ruchu palnika muszą być ściśle kontrolowane, aby zapewnić jednorodność i bezpieczeństwo spoin. Dla skomplikowanych spoin lub materiałów odpornych na pękanie może być konieczne zastosowanie technik pre-heat lub post-heat, aby zmniejszyć naprężenia wewnętrzne.
Znaczenie poprawnego zbrojenia
W kontekście konstrukcji żelbetowych poprawne zbrojenie odgrywa kluczową rolę w zapewnieniu nie tylko wysokiej wytrzymałości, ale również trwałości i bezpieczeństwa całej struktury. Zbrojenie żelbetowe składa się z prętów stalowych, które są odpowiednio rozmieszczone i połączone, aby współpracować z betonem w tworzeniu kompozytu o właściwościach mechanicznych idealnych do konstrukcji budowlanych.
Ważnym aspektem poprawnego zbrojenia jest jego dokładność geometryczna. Każdy element zbrojeniowy musi być ułożony zgodnie z projektowanym schematem, aby zapewnić równomierne obciążenie struktury oraz optymalną dystrybucję sił wewnętrznych. Przy niedokładnym rozmieszczeniu prętów grozi to nie tylko utratą wytrzymałości konstrukcji, ale także może prowadzić do nieprzewidzianych uszkodzeń w przypadku obciążeń dynamicznych lub katastrofalnych.
Proces montażu zbrojenia wymaga precyzyjnego wykonania, aby zapobiec pęknięciom betonu wokół prętów oraz zapewnić optymalne przyłączenie stali i betonu. Dzięki właściwemu zbrojeniu możliwe jest osiągnięcie pełnej wytrzymałości konstrukcji, co jest kluczowe dla zapewnienia bezpieczeństwa użytkowników i długoterminowej trwałości budynku.
Rodzaj zbrojenia | Zastosowanie | Właściwości |
---|---|---|
Podłużne pręty | Podstawowe zbrojenie nośne | Odporność na rozciąganie |
Zbrojenie poprzeczne | Wzmocnienie przeciwszczelinowe | Odporność na ścinanie |
Strzemiona | Wzmacnianie węzłów konstrukcyjnych | Zwiększenie sztywności |